トップ > ブログ > 記事
Blog
スタッフブログ
トップ > ブログ > 記事
ゴム練り加工の工程と配合剤や混練機の解説
ゴム練り加工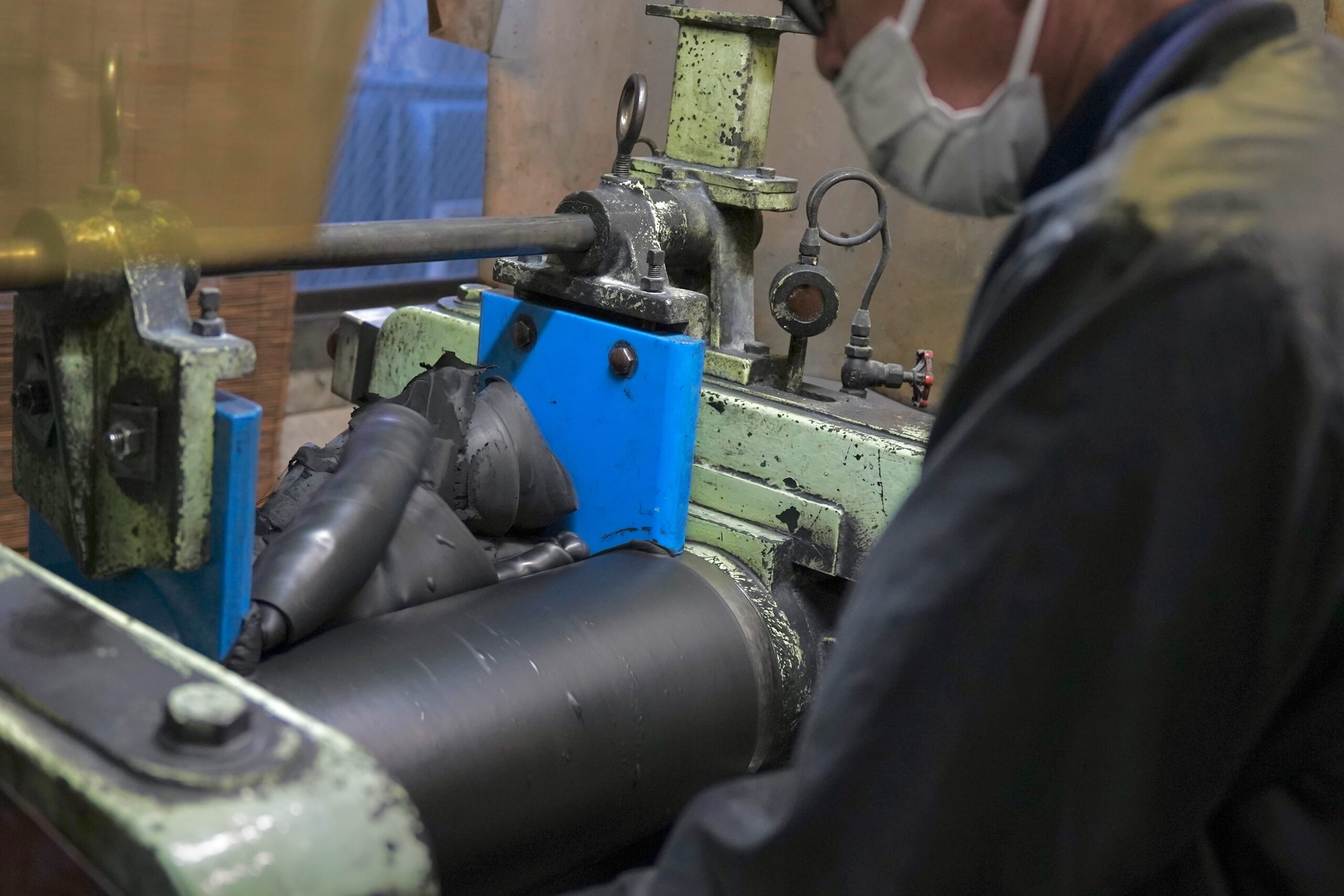
ゴム練りは、ゴム製品の品質を左右する重要な工程です。近年では、高機能ゴムへのニーズが高まっており、より高度な技術が求められています。
本記事では、ゴム練りで仕様する配合剤や工程、起こり得るトラブルについてまとめています。
ゴム練りとは?
ゴム練りとは、ゴム製品を作る際に、原材料であるゴムと配合剤を混ぜ合わせ、練り込む工程です。
高品質なゴム製品を製造するためには、原材料のポリマーに配合剤を混ぜ練り合わせるゴム練り加工が非常に重要です。
この工程は、ゴム製品の品質を左右する重要な工程であり、以下の3つの役割を果たします。
1. 原材料と配合剤を均一に混合する
ゴムは長い分子鎖でできており、そのまま配合剤を練り合わせても混合しにくい状態になっています。
そこで、まず素練りと呼ばれる工程でゴムのみを練り込み、分子鎖をある程度切断して側鎖を解きます。
その後、混練りと呼ばれる工程で、顔料などの配合剤を練り込み、ゴム材料全体に行き渡らせます。
2. ゴムを加硫しやすい状態にする
加硫とは、ゴム分子同士をを架橋と呼ばれる化学反応で結合させ、弾性や強度などを生み出す重要な工程です。
しかし、未加硫状態のゴムは分子鎖が絡み合っているだけで、十分な架橋反応が起こりにくい状態になっています。
そこで、ゴム練りによってゴムを加硫しやすい状態にすることで、加硫反応を促進し、より高品質なゴム製品を製造しています。
3. ゴム材料に可塑性を与える
可塑性とは、材料を曲げたり伸ばしたりすることができる性質のことで、ゴム練りによってゴム材料が柔らかくなり、成型しやすくなります。
ゴムは長い分子鎖でできており、分子鎖の長さが長ければ長いほど、可塑性が低くなります。そのため、ゴム練りにおいては、剪断力と呼ばれる力を加えて分子鎖を切断することで、可塑性を高めています。
ゴム練りの種類(素練り・混練り・分練り)
ゴム練りには、素練り・混練り・分練りの3種類があります。
それぞれ、使用する配合剤の種類や役割が異なるので、下記で詳しく見ていきましょう。
ゴム練りは3種類の工程に分かれています。
まず、素練りは原料ゴムに機械的なせん断力と可塑性を与える工程です。
後のゴム成型過程をしやすくする役割があります。
ロール機械を使用した作業では、効率よく作業を進めるために加工助剤の素練り促進剤の使用がされる場合もあります。
次に、混練りは原料ゴムと配合剤を練り合わせる工程です。
ニーダーマシンやロールマシンを使用して、ゴムに強度を持たせる役割があります。
最後に、分出しは練り込んだゴム材料を目的の大きさに寸法を合わせる工程です。
オープンロールを使用して作業します。
ゴム練りに使用する配合剤の種類と役割
ゴム練りに使用する配合剤には様々な種類があり、加工するゴム製品の特性に応じて配合剤を調整します。
代表的な配合剤には、以下の5つが挙げられます。
・ポリマー
・補強剤
・可塑剤
・加硫剤
・老化防止剤
ポリマー・・・
ゴムの原材料。
天然ゴム・ニトリルゴム・エチレンプロピレンゴム・フッ素ゴムなどさらに種類が分かれています。
補強剤・・・
ポリマーの物理特性に変化を与え、硬度や弾性を与える配合剤。
カーボンブラックなどが一般的です。
可塑剤・・・
硬さを調整する役割を担う配合剤。
オイル状の物が一般的です。
加硫剤・・・
ゴムを加硫させる(弾性力と耐久性をつける)ために必要な配合剤。
老化防止剤・・・
ゴム製品のオゾン劣化や屈曲疲労などを防ぐ配合剤。
ゴム練りに使用する混練機の構造と種類
ゴム練りに使用する混練機には次の4種類があります。
・オープンロール
・インターナルミキサー
・バンバリーミキサー
・ニーダーミキサー
それぞれの構造を詳しく見ていきましょう。
オープンロール
2つのローラーがついた構造で、練り込み速度が低速な混練機です。
素練りや配合剤を混ぜ合わせる作業で使用され、用途に合わせて手作業でゴムの厚みや大きさを調節することができます。
インターナルミキサー
密閉空間で圧力を加える構造をした混練機です。
噛み合い式のブレードが特徴的で、原材料との接地面積が広いため効率よく冷却することができます。
バンバリーミキサー
インターナルミキサーと類似した、密閉空間で圧力を加える構造をした混練機です。
圧力が高く、高速で材料を混ぜ合わせることができるので、大量生産に特化しています。
ニーダーミキサー
ニーダーミキサーは、密閉されたチャンバー内に回転するアームとブレードを備え、コンパウンドを強力にせん断することで練りを行います。
また、チャンバー内を加熱・冷却することで、コンパウンドの温度を制御することができます。
ゴム練り加工の工程
ゴム練り加工には2つの工程があります。
1.配合
2.素練り・混練り
それぞれの工程について詳しく解説していきます。
まずは、原材料のポリマーと配合剤を正確に計量します。
計量した材料を混練機を使用して混ぜ合わせます。
まず、インターナルミキサーやバンバリーミキサーなどの機械を使用して、素練りで原材料のポリマーに機械的なせん断力と可塑性を与えます。
次に、混練りでポリマーと配合剤をまぜ合わせます。
万が一、混練ムラや異物混入などのトラブルが発生すると、完成したゴム製品の品質に問題が生じる可能性があるので注意しています。
オープンロールを使用して、ゴムを薄いシート状に延ばします。
オープンロールを使用した成形であれば、ゴムを必要な厚さやサイズに柔軟に成形することが可能です。
ゴム練り加工に関するトラブル
続いてゴム練り加工で起こりがちなトラブルを3つご紹介します。
混練ムラ
均一なゴム練りができず混練ムラが発生すると、完成したゴム製品の品質や性能に悪影響が発生します。
具体的には、耐久・耐熱性を低下させ、摩擦に弱く破損しやすいトラブルが起こりがちです。
混練機の定期的なメンテナンスや材料の品質管理を徹底し、ゴム練り加工作業のプロセスを見直すことで、混練ムラを防止することができます。
ゴム焼け
熱・湿気・酸化などの外的要因が原因で、ゴム製品の品質や耐久性を損なうことをゴム焼けと言います。
ゴム焼けは、ゴム製品の不適切な保管が原因で発生しがちなトラブルです。
例えば、高温の環境でゴム製品を放置すると弾力性がなくなり、溶けたような状態になります。
また、ゴム製品は酸素・湿気・光に弱く、こういった環境下では白い粉が浮き出る、ひびが入る場合も。
ゴム焼けは、適切な保管方法で防止することができます。
異物混入
ゴム練り加工で原料や配合剤以外の、金属片・ゴミ・埃・化学薬品などが混入してしまうことを異物混入と言います。
異物が混入してしまうと目では確認できないので、弊社ではゴム練り後に金属探知機を利用するなどして異物混入を防いでいます。
まとめ
ここまで、ゴム練り加工の工程と配合剤や混練機の種類・構造を解説してきました。
ゴム練り加工はゴム製品を製造する作業で一番初めの作業です。
ゴム製品の特性に合わせて配合剤を調整することで、品質の高いゴム製品が完成します。
また、混練機は種類によって構造が異なるので、原材料や配合剤の特徴、製品生産量の用途に合わせて使い分けています。